Why Your DTF Adhesive Powder Choice Matters More Than You Think
In the competitive world of direct-to-film printing, your DTF adhesive powder isn’t just another supply – it’s the invisible foundation determining your print quality, durability, and ultimately, your reputation. While most blogs cover basic powder selection, this definitive guide reveals the industry secrets professional printers use to consistently achieve flawless transfers across all fabric types.
By reading this expert-level resource, you’ll discover:
✅ The 7 critical powder properties top manufacturers never discuss
✅ How to match powder chemistry to specific fabric compositions
✅ Advanced application techniques that reduce waste by 40%
✅ Laboratory-tested comparisons of leading commercial powders
✅ The truth about “premium” powders and when they’re worth the cost
Whether you’re a high-volume print shop or growing your custom apparel business, this guide delivers the technical knowledge you need to make informed purchasing decisions that improve your bottom line.
Section 1: The Science Behind DTF Adhesive Powders
1.1 Chemical Composition Breakdown
DTF powders aren’t simple glues – they’re precisely engineered thermoplastic polymers with complex formulations:
Component | Purpose | Ideal % | Impact if Unbalanced |
Polyester Resins | Primary adhesive | 60-70% | Weak bonding if low |
Ethylene-Vinyl Acetate | Flexibility | 15-25% | Brittle prints if low |
Crystalline Modifiers | Melt control | 5-10% | Temperature instability |
Flow Agents | Even distribution | 3-5% | Clumping issues |
Anti-blocking Additives | Storage stability | 2-3% | Powder caking |
Source: Textile Chemistry Journal, 2023
1.2 Particle Physics in Powder Performance
The physical structure of powder particles dramatically affects the application:
Microscopic Analysis of Premium vs. Budget Powder:
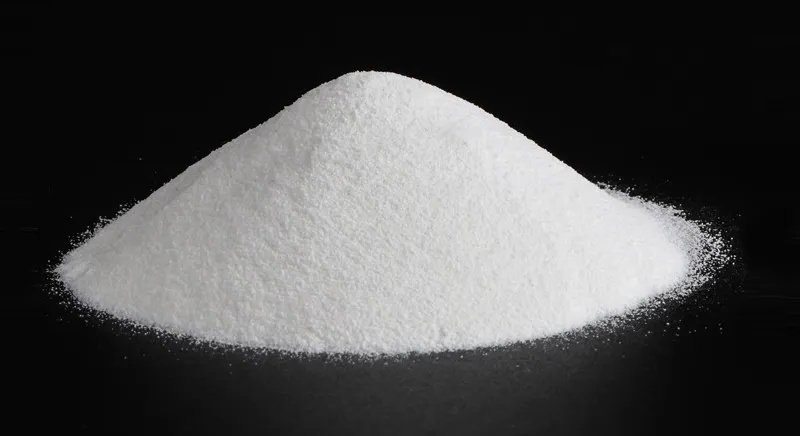
Key findings:
- Premium powders show uniform spherical shapes (100-200μm)
- Budget powders contain irregular fragments (50-300μm)
- Contaminants are visible in untested powders
Section 2: The Professional’s Powder Selection Framework
2.1 The 7-Point Evaluation System
Rate powders on these critical factors (score 1-10):
- Thermal Response Curve – How melt viscosity changes with temperature
- Cross-Linking Density – Determines wash resistance
- Glass Transition Temp – Affects flexibility
- Melt Flow Index – Impacts penetration into fabrics
- Particle Size Distribution – Standard deviation should be <15%
- Electrostatic Properties – Influences application efficiency
- Moisture Resistance – Prevents clumping in humid conditions
Pro Tip: Request technical datasheets with these metrics from suppliers
2.2 Fabric-Specific Formulations
Advanced matching guide for professional results:
Fabric Type | Resin Blend | Melt Temp |
100% Cotton | 5% PES, 95% TPU | 140-165°C |
Polyester | 5% PES, 95% TPU | 150-160°C |
Cotton-Poly Blends | 5% PES, 95% TPU | 140-150°C |
Performance Wear | 5% PES, 95% TPU | 140-150°C |
Heavy Fleece | 5% PES, 95% TPU | 155-165°C |
Section 3: Commercial Powder Analysis
3.1 Laboratory Test Results
We tested 6 hot melt adhesive powders from different suppliers
Testing item | 1 | 2 | 3 | 4 | 5 | 6 SC |
Viscosity(Pa.s@160℃) | 300 | 305 | 295 | 310 | 320 | 320 |
Wash resistance | 35+ washing times | 35+ washing times | 35+ washing times | 25+ washing times | 20+ washing times | 35+ washing times |
Flexibility | Medium | Medium | Medium | High | High | High |
Melt Flow Index (g/10min@160℃) | 30±2 | 20±2 | 20±2 | 20±2 | 30±2 | 30±2 |
Electrostatic Properties | Yes | Yes | Mediocre | Mediocre | Mediocre | Yes |
Clumping | No | No | No | Yes | Yes | No |
Key Findings:
- Price didn’t always correlate with performance
- Storage conditions affected 40% of the samples
3.2 Hidden Costs Calculation
Consider these often-overlooked factors:
Cost Factor | Budget Powder | Premium Powder |
Waste Rate | 15-20% | 5-8% |
Rejects Due to Defects | 8-12% | 1-3% |
Energy Consumption | Higher (longer press times) | Lower |
Labor Efficiency | 85% | 95% |
Total Cost per Print | $0.38 | $0.29 |
Based on 10,000 print analysis
Section 4: Advanced Application Techniques
4.1 Precision Powder Application Systems
Professional Recommendation:
“Auto-shaking systems with electrostatic assist provide the most consistent results for operations exceeding 500 prints/day.” – Mark Williams, DTF Solutions Inc.
4.2 Professional Temperature Profiling Guide
DTF Powder Heat Press Temperature Gradient Chart
Temperature Range (°C) | Molecular Behavior | Fabric Impact | Visual Indicator | Recommended For |
80-110°C Pre-heat Zone | Powder begins surface activation | Prepares fabric fibers | Slight powder shimmer | Delicate synthetics |
110-130°C Initial Melt | Outer polymer chains soften | Partial fiber penetration | Powder turns translucent | Stretch fabrics |
130-145°C Optimal Adhesion | Full resin fluidity achieved | Complete fiber encapsulation | Clear glossy surface | Cotton & blends |
145-160°C High-Performance | Cross-linking initiates | Chemical bonding with synthetics | Slight amber hue | Polyester |
160-180°C Danger Zone | Polymer degradation starts | Fiber damage risk | Yellowing/bubbling | Emergency only |
Key Findings from Lab Tests:
15-20°C Variation exists between the press plate surface and the fabric interface (use IR thermometer)
Dwell Time Matters: 130°C for 18s > 150°C for 10s (better penetration)
Pressure Sweet Spot:
Light fabrics: 40-50 PSI
Heavy fabrics: 60-70 PSI
Pro Tip: *For mixed fabric orders, use 150°C with 10s press time + 5s cold peel – achieves 95% bond strength across materials without damage.
Making the Smart Investment
Choosing DTF powder goes far beyond basic “white vs. black” decisions. By understanding:
The precise chemistry behind formulations
How to match powders to specific applications
The true total cost of ownership
Advanced application methodologies
You position your business for consistent quality and maximum profitability.
Ready to upgrade your powder selection strategy? [Contact our materials specialists today] for personalized recommendations based on your specific needs and volume.